[Part 1] From raw hide to leather
We visited the tanner who tans the leather that makes dünn leather, and the vendor who entrusts us with the foil stamping of CARDRIDGE.
The salted hide is up close. Leather is, after all, made from living things.
We know that leather is made from animals because we hear things like cowhide and pigskin. However, few people may be able to imagine that leather is actually made from animal skin by looking at the beautifully shaped leather that has arrived in front of our eyes. not. So this photo may be a little shocking. Dairy cow hides are folded and piled up here.
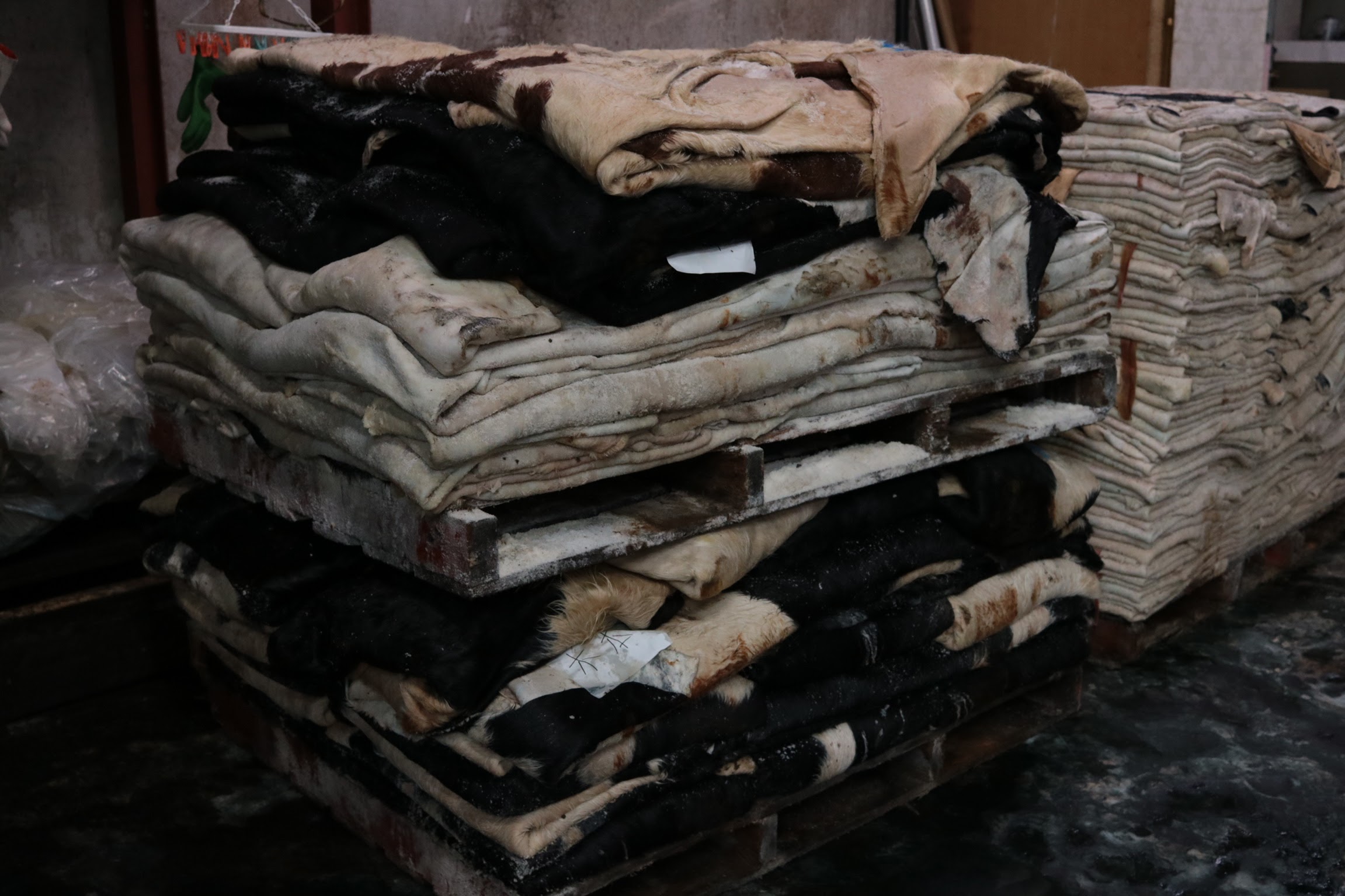
This one is salted. Apparently it's for preservative purposes. It's flatter than the previous one, probably because the water has been removed.
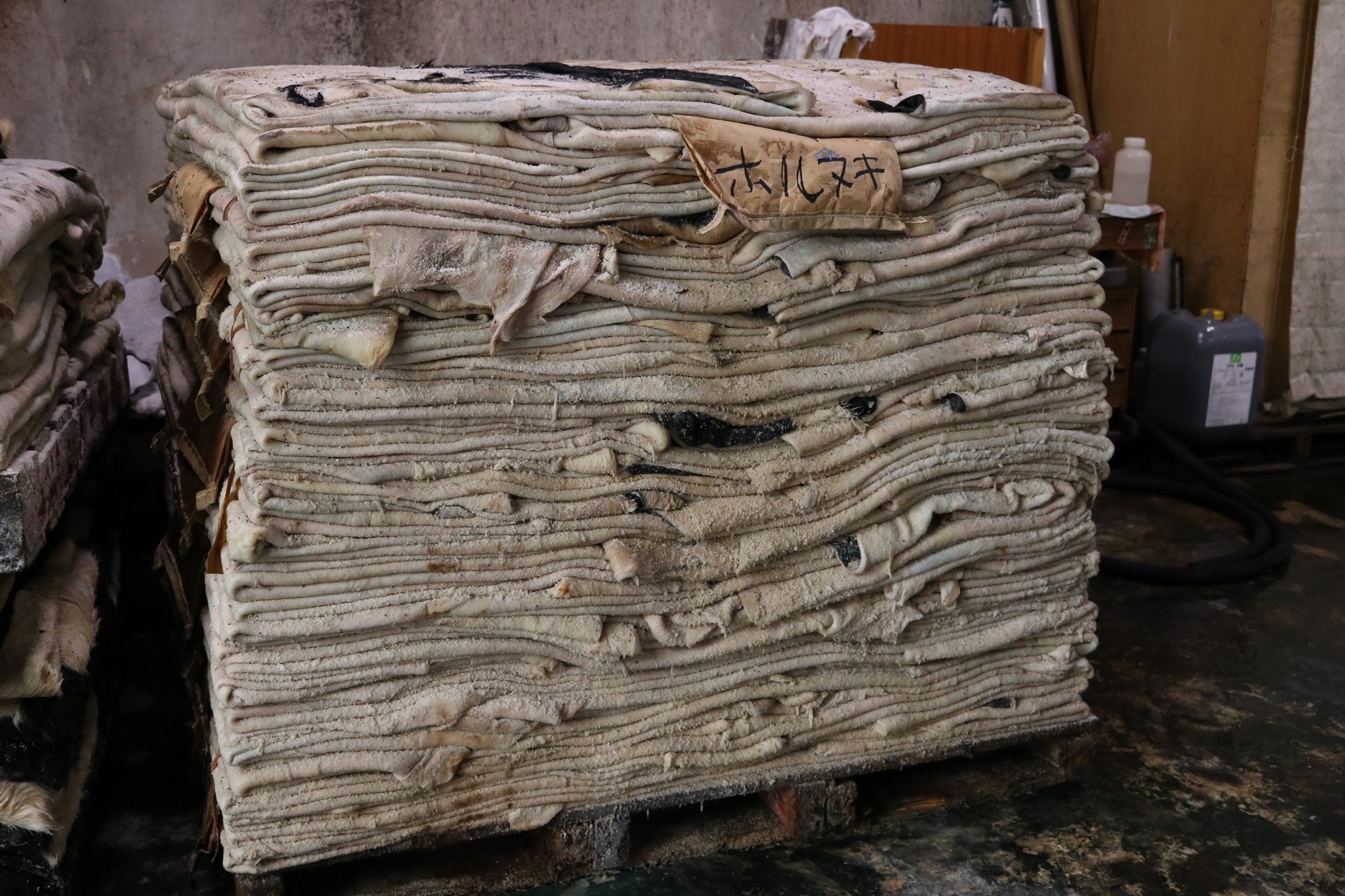
If you look closely, you can see large grains of salt sprinkled on it.
When the hide is tanned with chrome, it turns into a beautiful light blue color. This is called wet blue.
When the raw leather mentioned earlier is processed with chrome tanning (a type of metal tanning), it turns light blue due to the effect of the tanning agent.
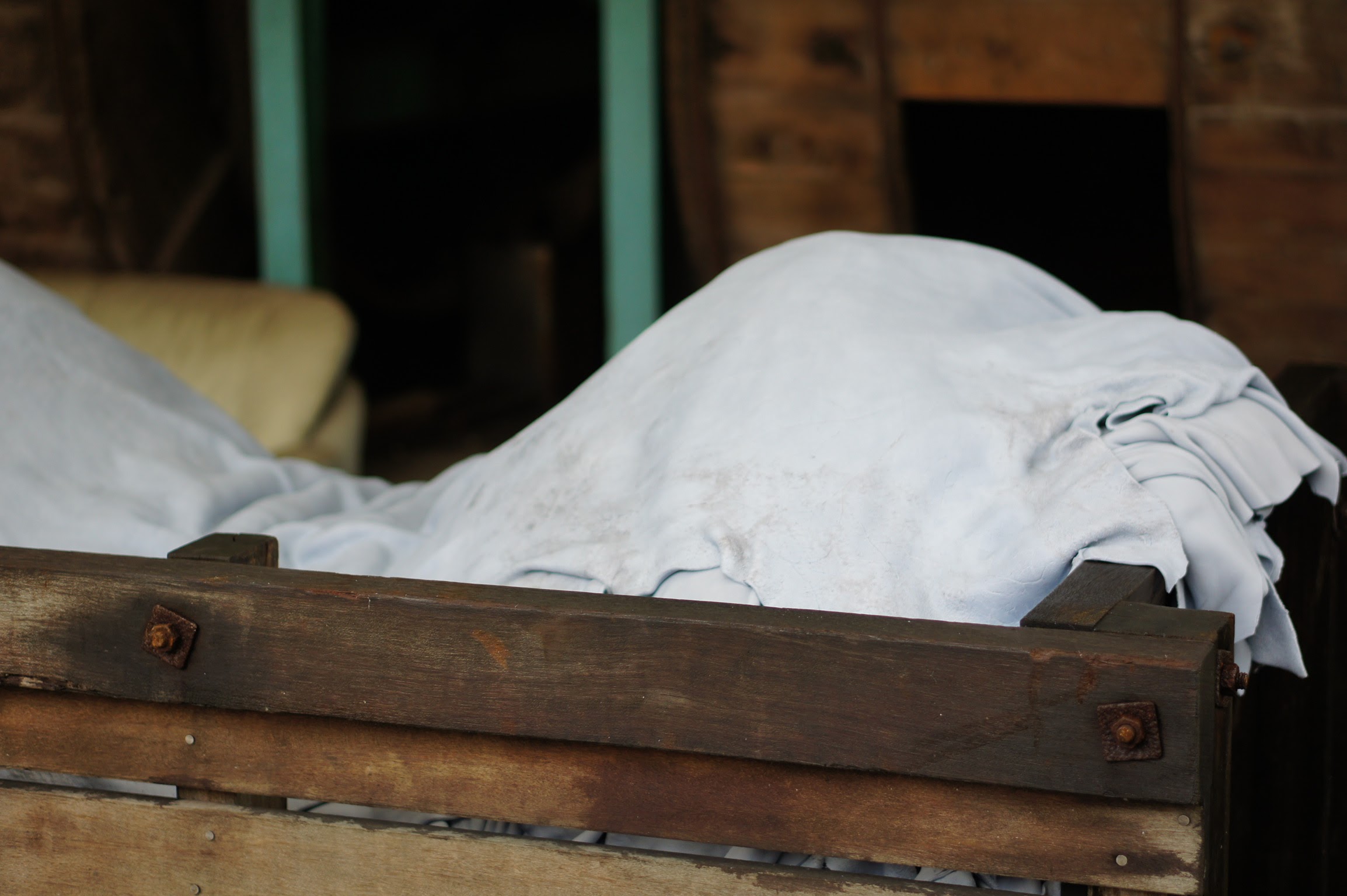
It's supple leather.
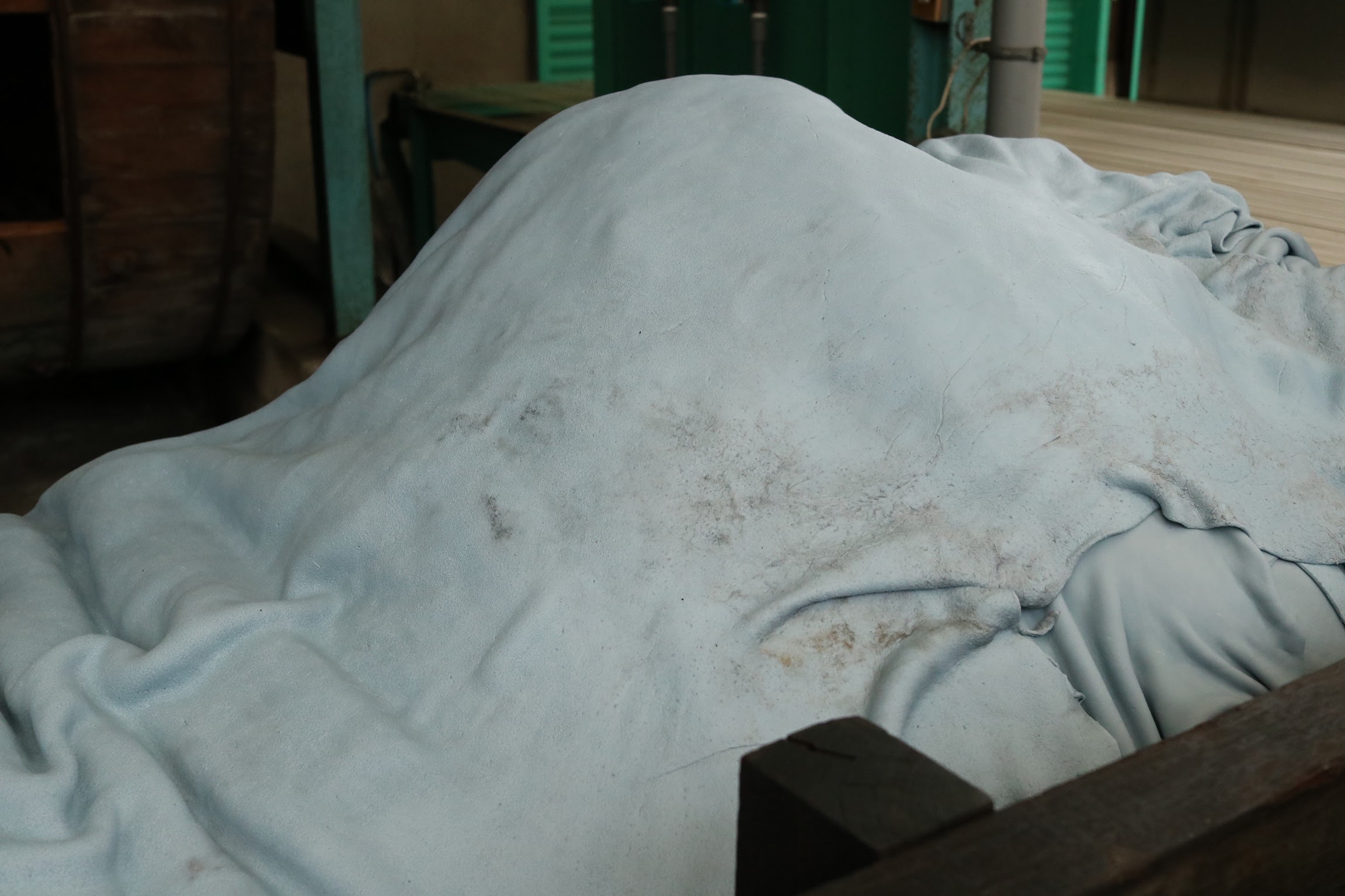
It feels fluffy to the touch.
In chrome tanning, the leather is colored in a drum.
Color is applied to the leather using a drum-type dyeing machine. The craftsman takes out the leather just like taking out laundry and carefully stacks it one by one.
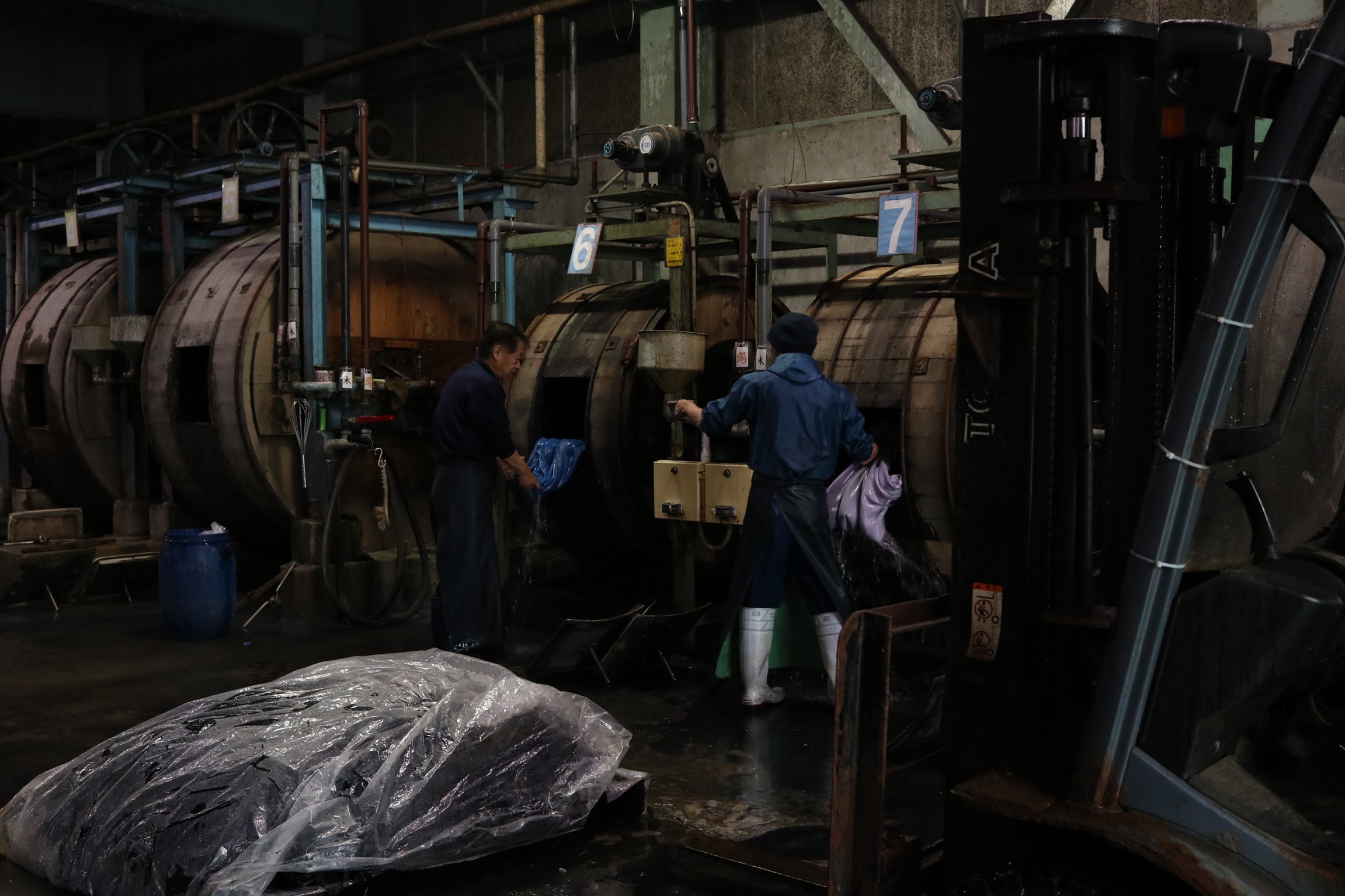
It is dyed a beautiful blue. dünn leather is dyed using this method.
Another dyeing method using a roller that is not used on dünn leather.
Pass the leather through a dyed roller and it will instantly become colored. It's freshly painted so it's shiny.
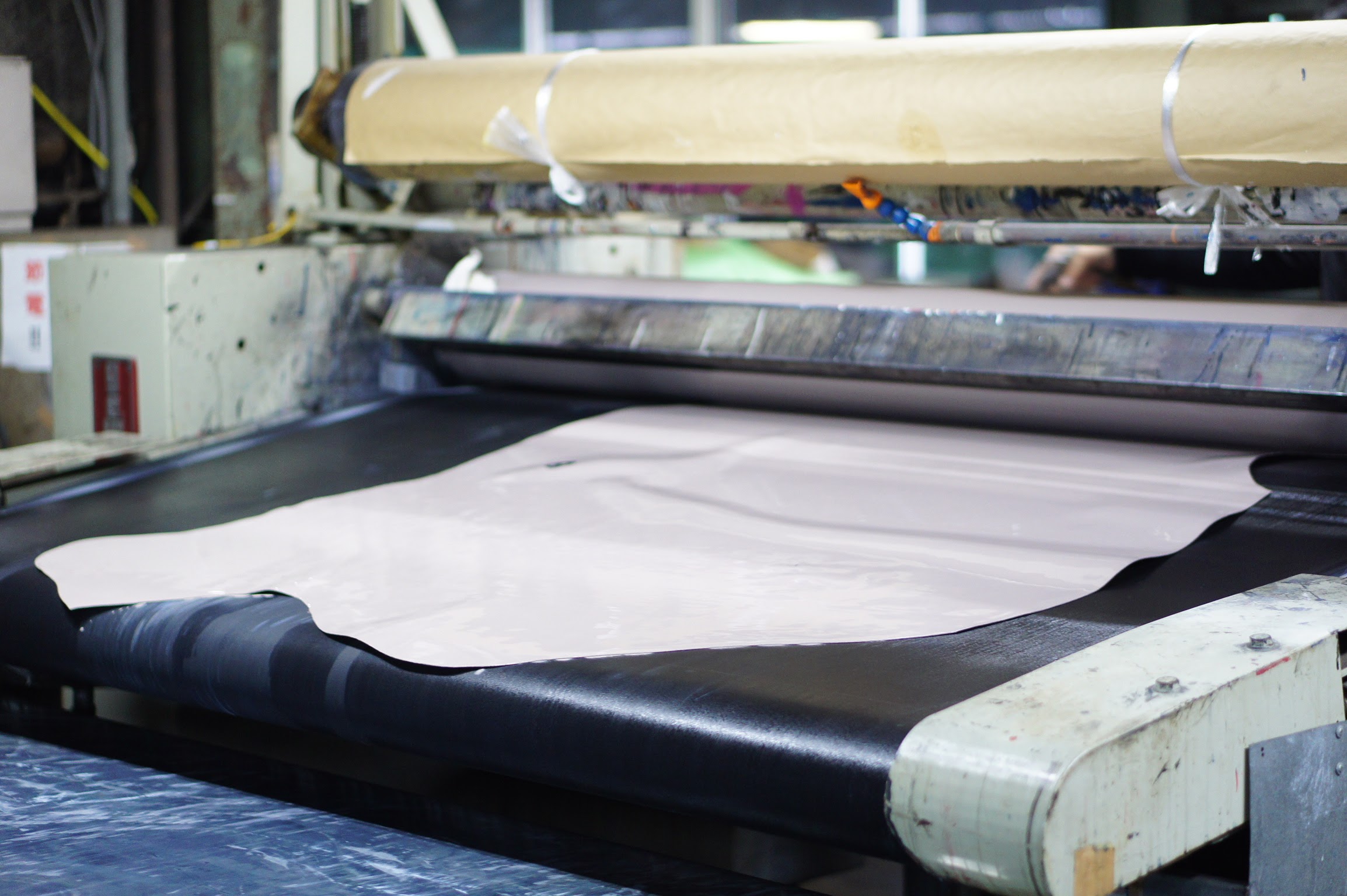
This is then dried in a long dryer, and finally hung to dry.
various leathers. It is the prototype of a famous product.
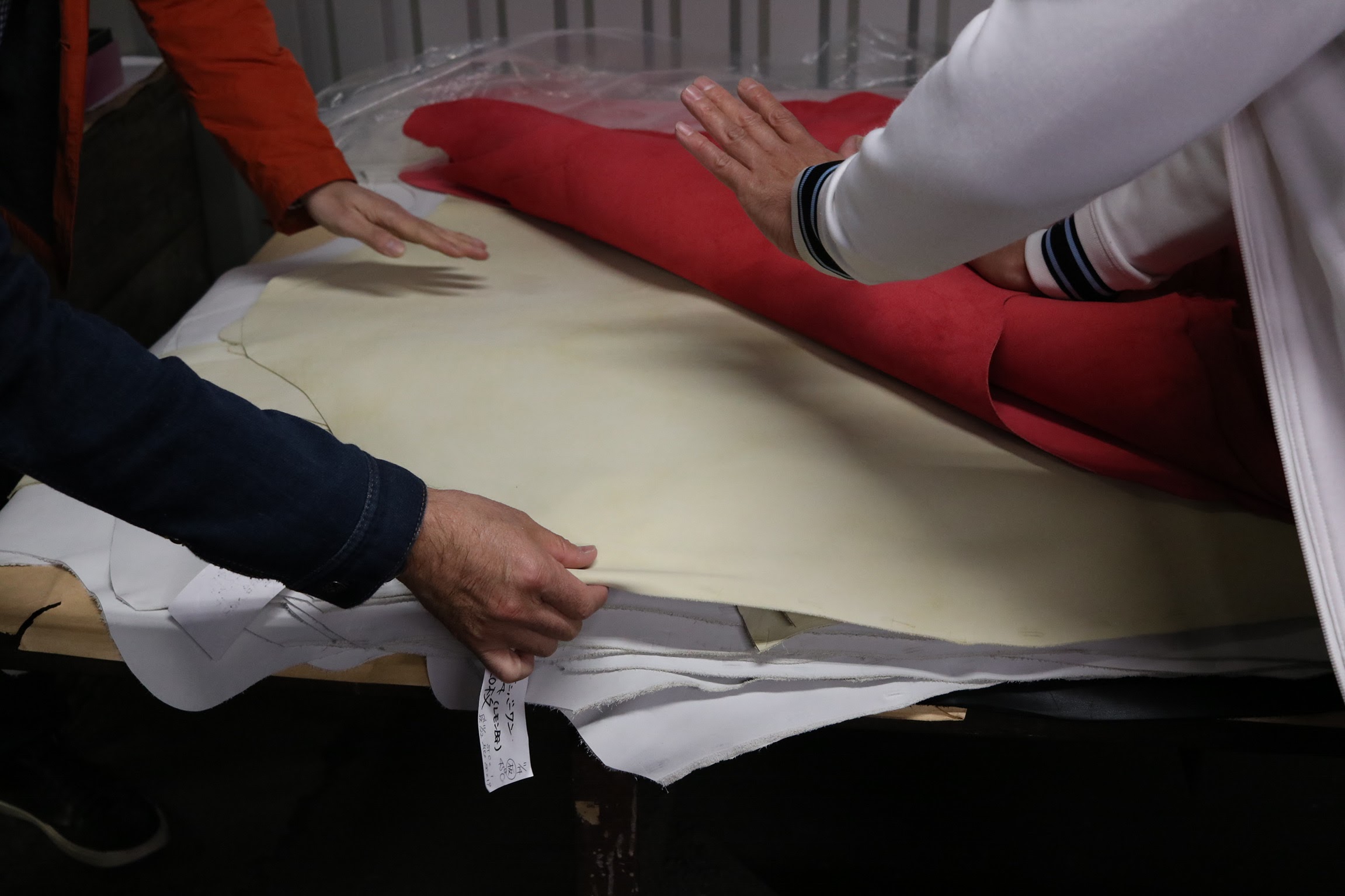
The white leather underneath this red is the unfinished leather used in the dünn series. It was moist and soft to the touch. Also, this is velor. For dünn leather, the side with the hair is called the silver side, but with velor, the side with the flesh is called the floor side. This one is fluffed and feels smooth to the touch.
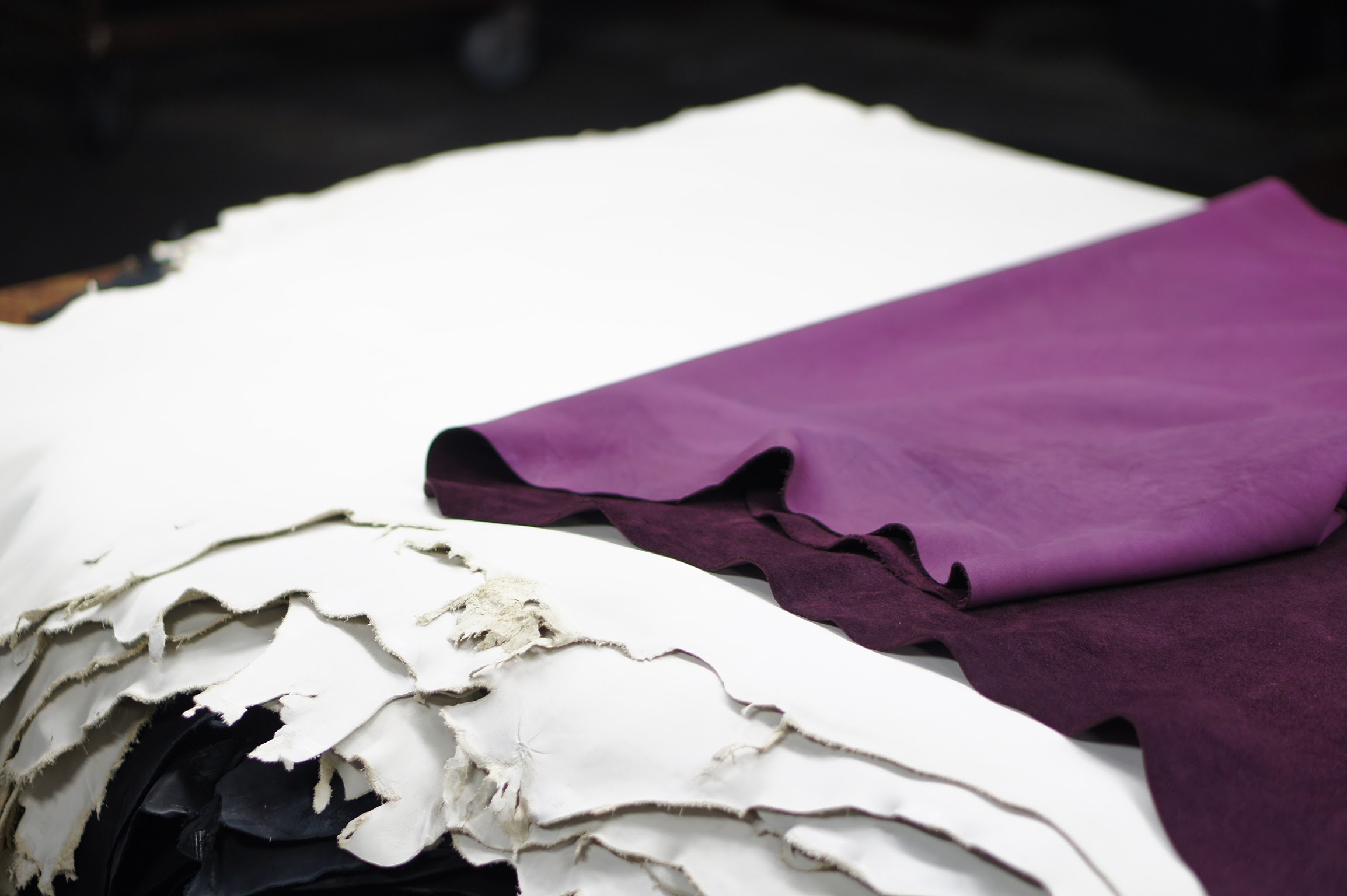
Even with the same leather, the texture can be so different if the process is different. I was impressed by the experience, which can only be understood by experiencing it on site.
[Part 2] The expression can change infinitely depending on how you finish it!
The type of roller determines the texture of the leather.
This big machine. Three huge rollers are set inside this.
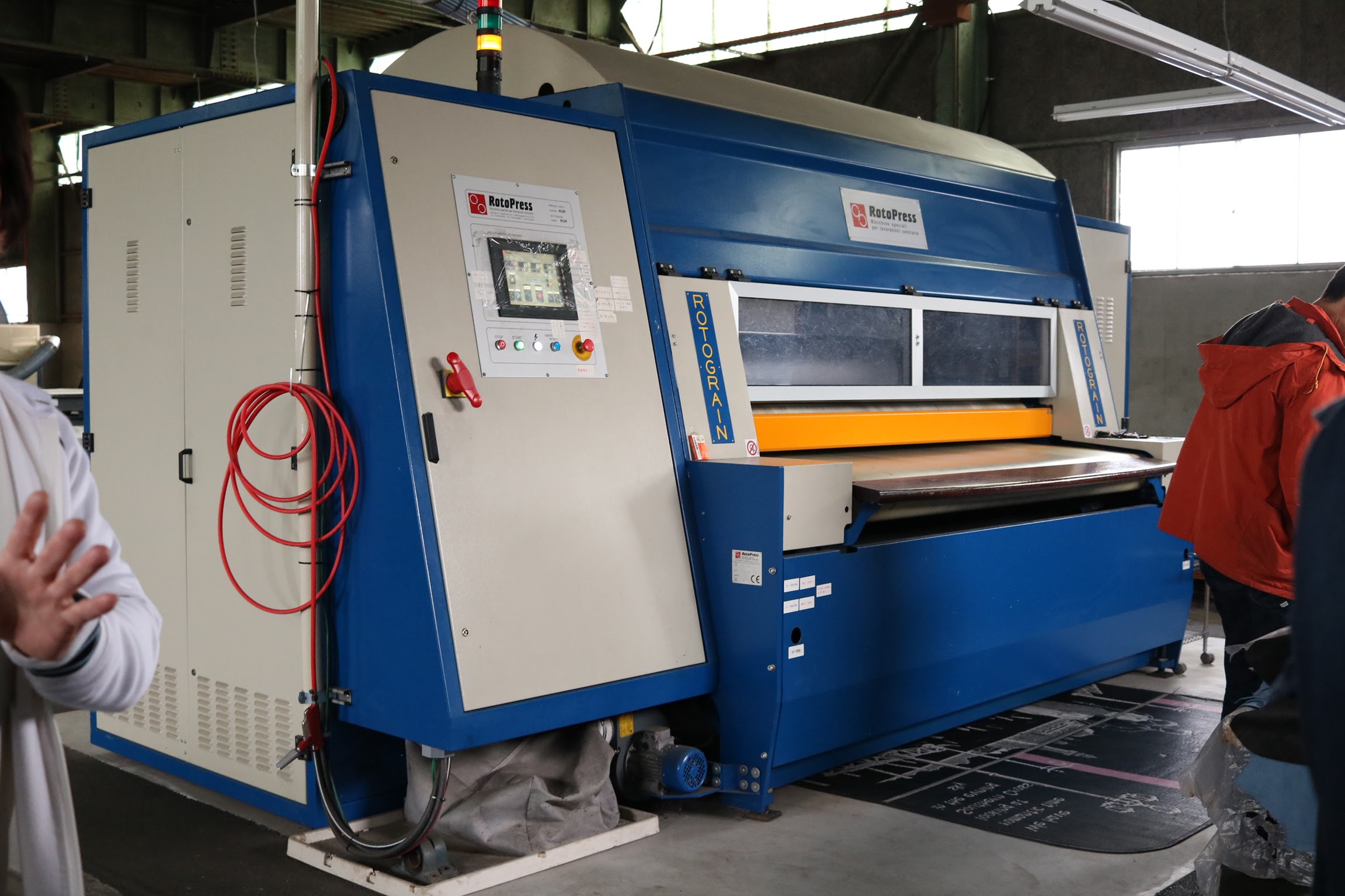
From above, blue, silver, and black rollers. Each leather has a different surface texture, and you can change the appearance of the surface by running the leather through this roller.
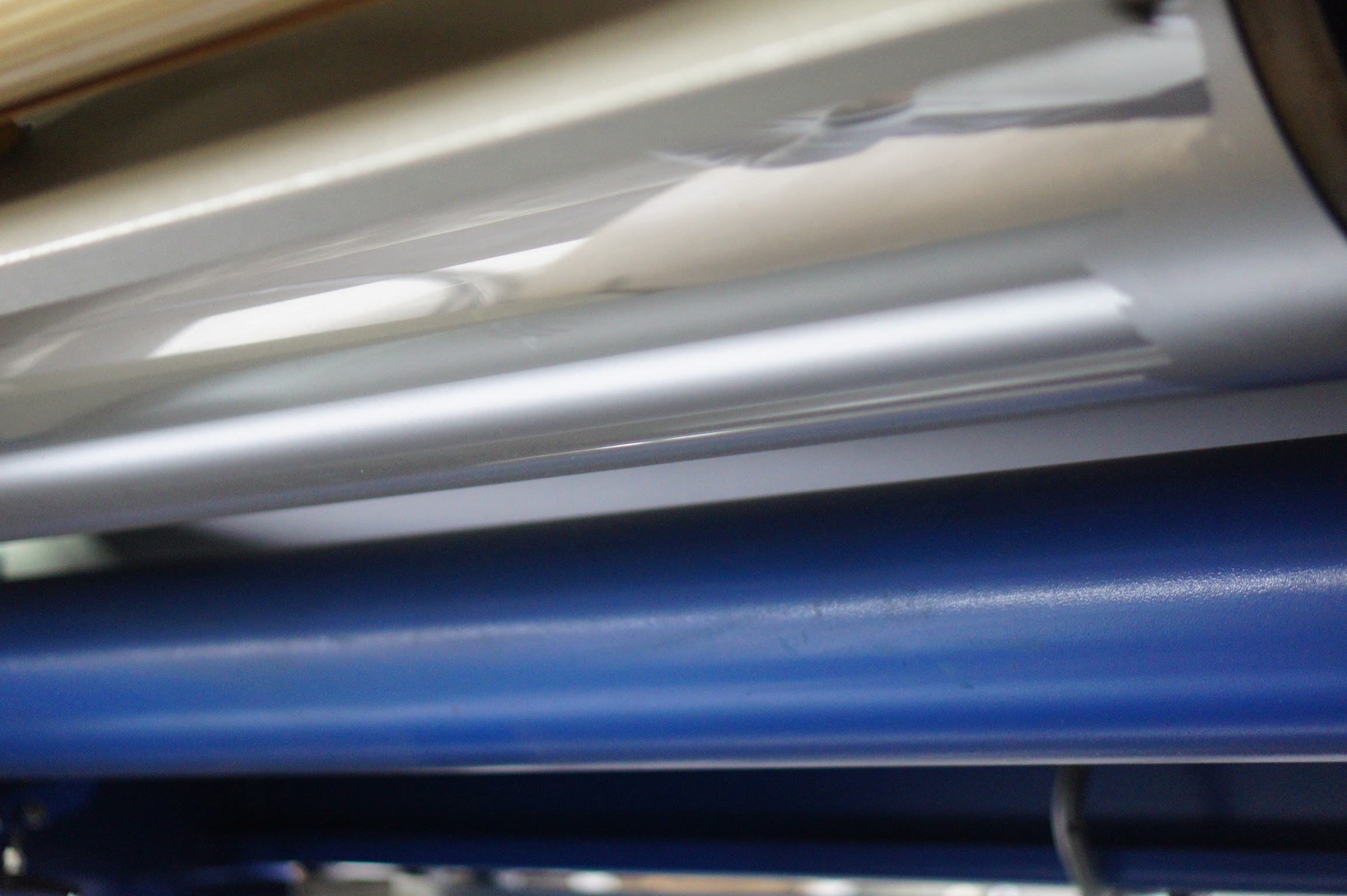
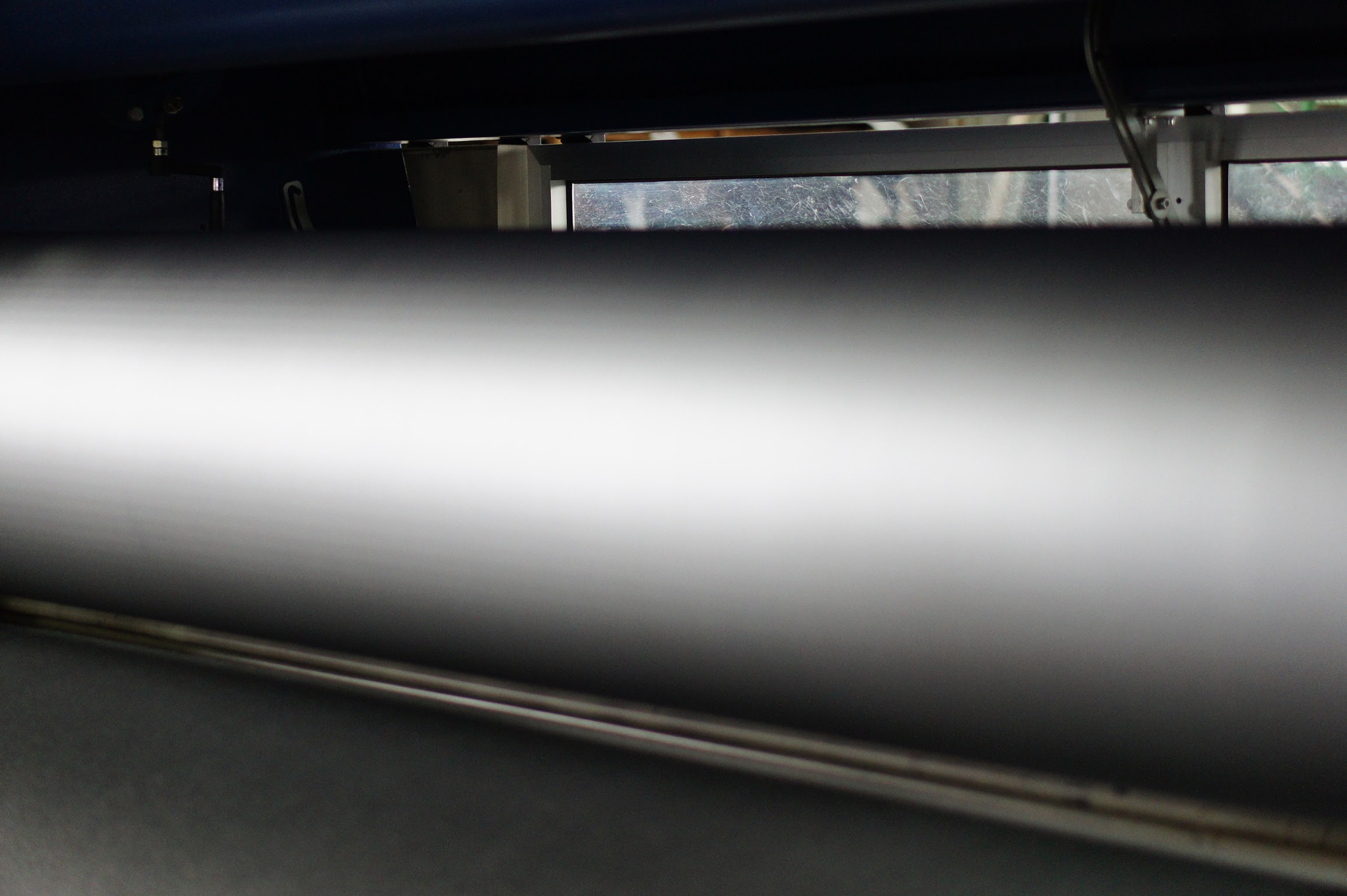
Dry in the shade in a well-ventilated place.
The wind was blowing strongly that day, and a large amount of leather was waving around. It's spectacular.
And then to the product.
The leather that reaches us is made through many processes like this. The amount of water used to tan the hide of one cow is a whopping 2.5 tons. Leather should not be allowed to get wet after drying, but the manufacturing process uses a lot of water. The leather, which has been painstakingly made by craftsmen, has a moist and glossy luster, and just looking at it gives you a mysterious, soothing feeling. And dünn uses this finished leather that is thinner and thinner. Its thinness is 0.5mm.
I previously covered the process of thinning this leather. Many of the products in the dünn series are compact, but many of these craftsmen have poured into them extremely detailed techniques. When you are lucky enough to pick up a dünn, please think about that background. We hope that you will feel that dünn, which fits in the palm of your hand, is something special.